Understanding the Steel Die Cutting Process for Packaging
At The BoxMaker’s corrugated production facility just outside of Seattle, WA, we are capable of producing just about any item on your corrugated wish list — from a tiny mailer for headphones to a king-sized mattress box.
Many standard box styles (think typical square shipping boxes or similar) can be print, cut, and glued if necessary on a single machine, without the need for additional tooling. This keeps your costs at a minimum.
However, whenever your custom packaging design includes additional features like curves, angles other than 90 degrees, cutouts (such as windows or hand holes), or perforation, the use of additional tooling is most likely required to complete the job. For high volume orders, this additional tooling is typically a specially made steel die.
What is a Steel Die?
With its origins in the shoemaking industry dating back to the Industrial Revolution, the process of die cutting played an important role in the growth of mass production. In the 21st century, die cutting has evolved into a versatile fabrication process that uses specialized machines and tools to convert stock materials into custom shapes and sizes.
A steel die (also known as a cutting die) is essentially a giant cookie cutter made specifically for your product. Corrugated boxes and other packaging products are often produced using a custom steel die on a die cutting machine. This rapid manufacturing process not only speeds up production, but also ensures each finished product delivers a consistent result every time.
Steel dies are made with steel rule – long strips of steel approximately an inch wide – which are pounded into ultra-hard ironwood in the exact shape that a structural packaging designer creates for your product. Different types of rule are used to create different outcomes, such as a perforated or standard box score.
What is the Cost of a Steel Cutting Die?
The cost of a steel die can vary greatly depending on how intricate your packaging design is, what machinery your die is made for, and how many impressions will be stamped at one time. Since each piece of steel is hand-pounded into the body of wood, the more intricate your design, the more steel and labor is required to make your cutting die, resulting in a higher cost. Prices typically range from $250 to $3,000.
Keep in mind that your steel die is a one-time only charge*. The material used to make a cutting die is high quality and built to last, so your manufacturer can produce many orders over the years using the same steel die. Ultimately, the initial cost of the steel die will offset over time with repeated orders. Learn more about how to calculate the cost of packaging.
*Check with your packaging manufacturer to find out how long they will store your die for future use.
How is a Steel Die Made?
Steel dies can be costly due to the high-tech machinery, top notch materials, and specialized skilled labor required for their manufacture. These complex tools are typically custom made in a matter of days, depending on your packaging provider.
To better understand how the steel dies work, take a journey through The BoxMaker’s creation process from design conception to the finished die:
Step 1: After a project order is submitted, The BoxMaker’s structural design team creates a computer-aided design (CAD) drawing and sends it to our local die cutting manufacturing partner.
Step 2: The die cutting manufacturer uses a laser cutter to burn the drawing into the wood. Our design team indicates on the CAD drawing what type of steel rule is needed for each portion of the product. There are many different rule options, each one built to accommodate the specific corrugated thickness, flute size, and type of action the rule needs to perform – a score, perforation, a slit-score, or cut, to name a few.
Step 3: The die cutting manufacturer prepares a file to be sent through the Rule Bender. The Rule Bender cuts, bends, and notches the steel into the specific length and shape needed.
Step 4: The bent and cut rule are manually pounded into a laser-cut board. A portion of the steel rule has been inserted into this small flatbed die with intricate shapes. The more detailed designs require more labor, and sometimes hand-bending each piece of rule. Then, the operator pounds in the steel rule into the wood of this rotary die with a rubber mallet — a laborious and taxing step in the creation process.
Step 5: After the steel has been pounded into the wood, foam rubber pieces in different densities and heights are glued onto the die. These various pieces of foam help the die to bounce off the corrugated board. The grey foam surrounds the rule to allow for the corrugated to push off of the rule, and the cream foam is used so that the corrugated scrap will pop out after being cut.
Step 6: We create a sample of the die, known as a pound-off, and compare it to the original CAD drawing before the order is run to make sure that the die is exactly what our client is looking for.
Flatbed Die-Cutters vs. Rotary Die-Cutters: What’s the Difference?
There are two different types of machines that use cutting dies — flatbed die-cutters and rotary die-cutters. Flatbed dies are made with a flat, rectangular piece of hardwood, where the wood for a rotary die wood board is curved in shape. As a result, the method for making rotary steel dies is more extensive.
Flatbed dies have a smaller “blank” size (meaning they can’t be used for very large designs). However, they are more capable when it comes to intricate details such as small cut-outs, tight corner radiuses, and slit scores. Rotary steel dies have a larger blank size and can convert more boxes per hour.
Selecting the right die cutting method is not a “cut” and dry decision. With many factors at play, such as cost, order size, and special packaging requirements, your packaging manufacturer will select the type of die used on your project based on their machinery and the best fit for your specific structural design and project needs.
Digital Cutting and Finishing as a Steel Die Cutting Alternative
Advances in technology mean that some box converting has gone digital. Digital CAD tables from manufacturers such as Zünd and ESKO deliver an automated die-less finishing system for packaging and point-of-purchase displays. These digital cutting tables and those like them utilize computer-controlled cutting heads or lasers to rapidly convert full sheets of corrugated into individual boxes or displays. Digital converting can be a good option for low to mid-size order volumes. While this method is not yet as fast as analog die cutting, it does not require the manufacture and purchase of a steel die.
Partner with Your Custom Packaging Provider
If you have any additional questions about cutting dies or the steel die cutting process, consult with our experienced Packaging Advisors. We can help determine the most effective converting method for your brand, while considering your bottom line and desired packaging outcome.
The BoxMaker can produce an extensive range of custom corrugated packaging to fit your needs. From food and beverage to the medical device industry, we work with brands throughout the Pacific Northwest and beyond to bring their packaging vision to fruition. Schedule a free consultation today.
Subscribe
Share this post
Similar Articles
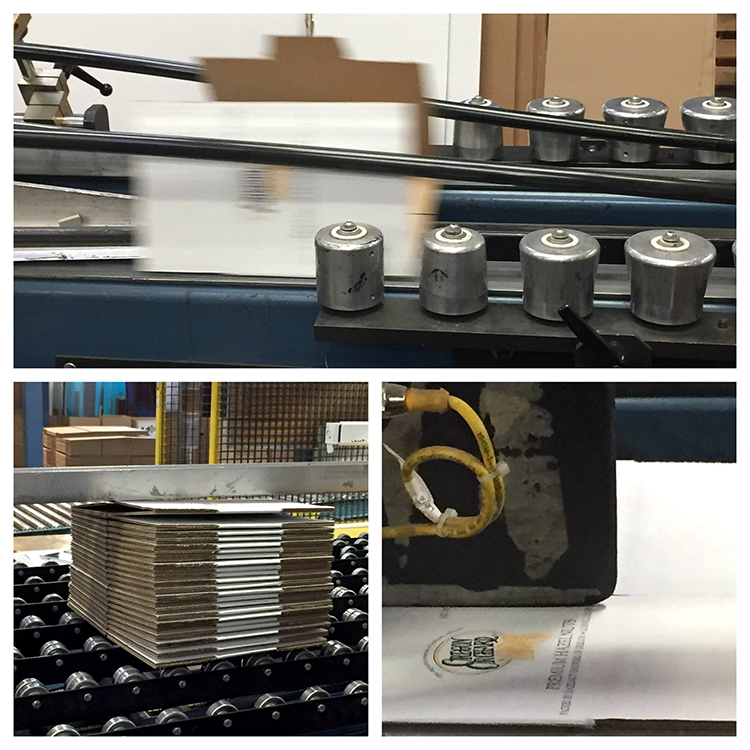
Packaging Overruns & Underruns Explained
Learn about packaging overruns, packaging underruns, why they happen, and the custom packaging manuf …
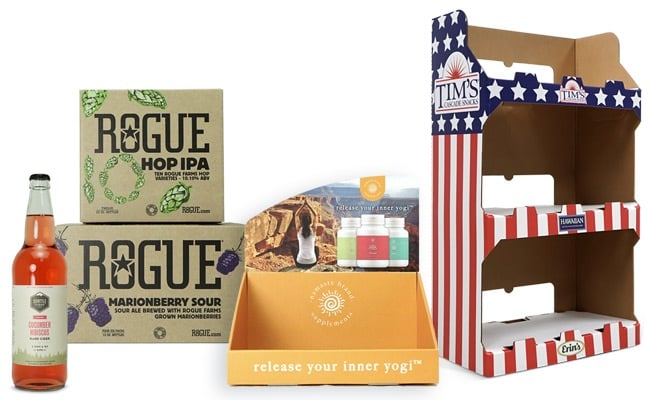
Litho Lamination vs. Digital Print for Retail Packaging
Learn about comparing Litho Lamination vs Digital Print and how technological advancements in digita …
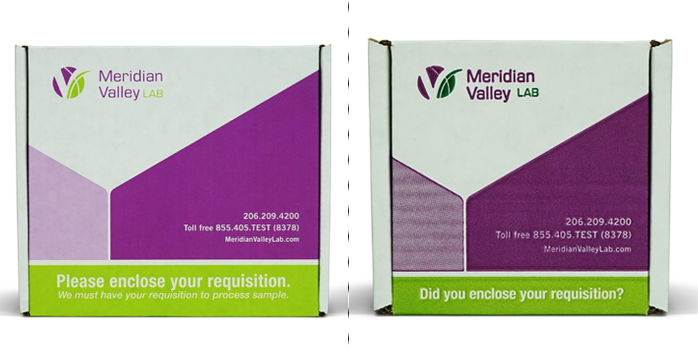
Making the Upgrade from Flexo to Digital Print
Switching from flexo print to digital print is no easy decision. Here are three reasons to make the …